Beyond Cheap Labor: Building America's Smart Manufacturing Workforce
How Intelligent Workers Are American Manufacturing's Greatest Competitive Advantage
June 19, 2025
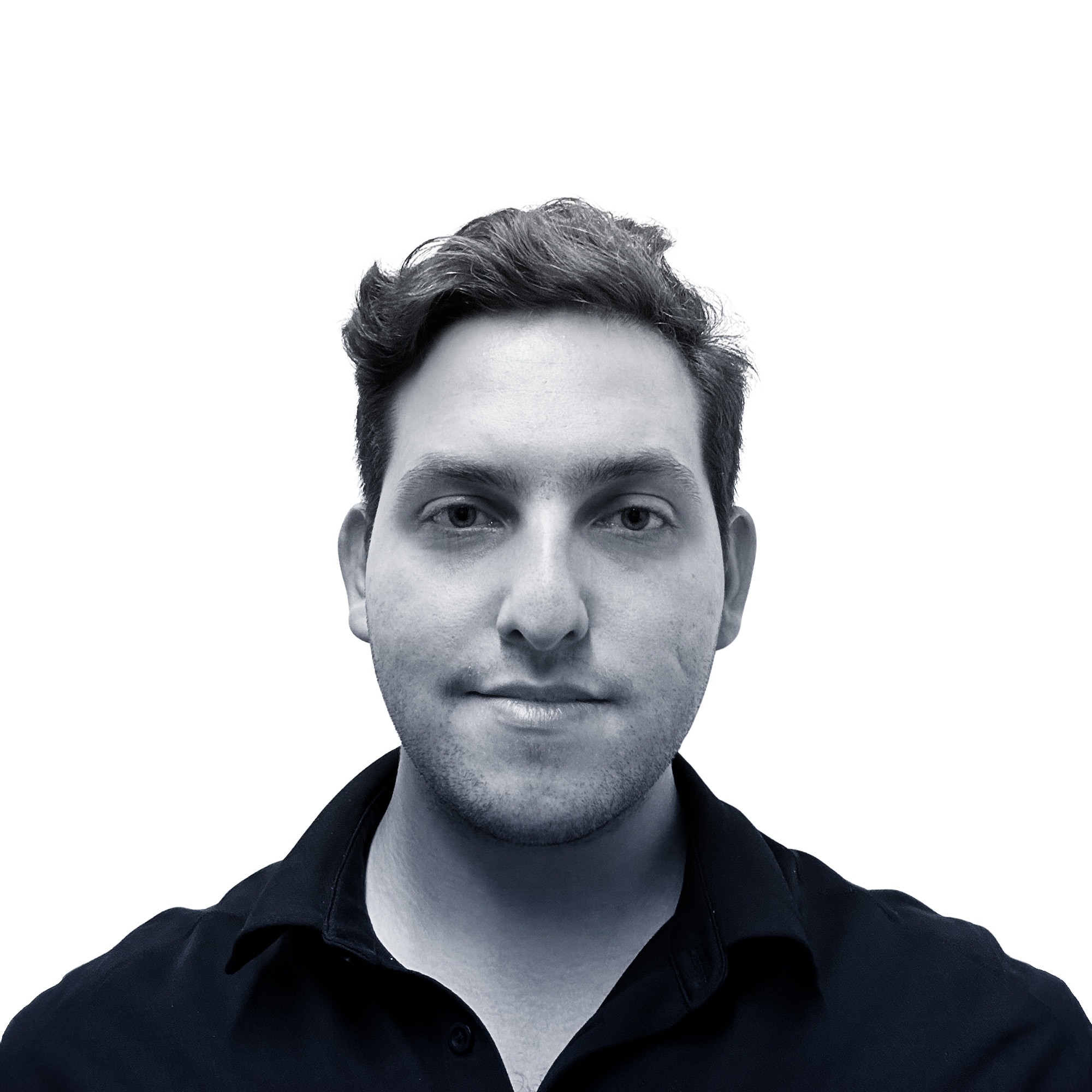
For decades, American manufacturing strategy could be summarized in a simple, if uncomfortable, equation: if labor costs rise domestically, move production to where labor is cheaper. This approach sent millions of manufacturing jobs overseas and hollowed out industrial communities across the country. Companies chased ever-lower wages across the globe, from China to Mexico and beyond, in what seemed like an endless race to the bottom.
That era is fast coming to an end. Today, several converging factors are forcing a fundamental rethinking of how manufacturers think about their workforce, staffing and geography.
First, the labor cost advantage of traditional offshoring destinations is eroding. Average salaries in China have more than doubled over the last decade, following the country's rapid growth in GDP and living standards. The pure wage arbitrage that drove offshoring is delivering diminishing returns.
Second, the hidden costs of extended supply chains have become increasingly apparent. Supply chain disruptions cost organizations an average of 6-10% of annual revenues, with some studies showing disruptions causing $1.6 trillion in missed revenue. The COVID-19 pandemic and subsequent supply chain crisis delivered this lesson with brutal clarity.
Third, manufacturing itself is evolving. As production becomes more customized, high-mix and technology-intensive, the competitive advantage shifts from low-cost repetitive labor to high-value knowledge work. The factories of the future require fewer hands but more brains.
These shifts point to an inescapable conclusion: America cannot rebuild a robust manufacturing base by competing on labor costs. It must instead compete on labor value, developing a workforce that may be smaller in number but vastly more productive and innovative. In other words, if we can't be cheaper, we must be smarter.
From Quantity to Quality: The Smart Labor Approach
The smart labor approach to manufacturing represents a fundamental shift in how we think about manufacturing workforce development. Rather than viewing workers primarily as a cost to be minimized, this approach sees them as a value to be maximized. This perspective changes everything from recruitment to training to work design.
At its core, smart labor in a manufacturing context is about amplifying human capabilities through technology, knowledge and workplace design. It means equipping workers with the tools, information and authority to solve problems, improve processes and drive innovation. It also involves creating a manufacturing environment where human expertise, experience and judgment paired with automation technologies become competitive advantages.
This approach is gaining traction across American manufacturing. Companies are recognizing that in a world where basic production can be automated or offshored, the real value comes from workers who can handle complexity, solve novel problems and continuously improve manufacturing operations.
The smart labor model manifests in several key shifts in workforce strategy:
- From repetitive tasks to problem-solving roles: Jobs are being redesigned to eliminate routine work (through automation) while expanding responsibilities for process improvement, quality management, and technical troubleshooting.
- From narrow specialization to versatile expertise: Workers are being trained across multiple disciplines, creating more flexible teams that can adapt to changing production needs.
- From following procedures to improving them: Employees at all levels are being engaged in continuous improvement, contributing their insights to refine processes and eliminate waste.
- From isolated work to collaborative innovation: Cross-functional teams bring together different perspectives to solve complex manufacturing challenges and drive innovation.
- From limited information to data-rich decision making: Workers are given access to real-time production data and analytics, enabling more informed decisions on the factory floor.
These shifts represent a profound change in what it means to work in manufacturing. The smart labor approach doesn't just change what workers do, it changes how they think about their role in the production process.
Technology as a Force Multiplier
A key element of the smart labor approach is using technology not to replace workers, but to amplify their capabilities. Advanced technologies are being deployed as force multipliers that enable a smaller workforce to achieve greater output, quality, and innovation.
Digital work instructions stand at the forefront of this transformation. The impact of digital work instructions is substantial and measurable. Companies implementing digital work instruction systems have seen significant improvements. For example, a study in the Journal of Operations Management found that subjects using digital work instructions made approximately half as many mistakes compared to those using paper-based instructions. In terms of overall productivity, some companies have reported efficiency increases of up to 95% with digital work instructions.
Similar benefits are being realized through other smart manufacturing technologies:
- Factory Automation Technologies that digitize and automate core manufacturing workflows
- AI-powered decision support systems that analyze complex data and provide recommendations to human decision-makers
- Collaborative robots (cobots) that handle repetitive or physically demanding tasks while working alongside human operators
- Knowledge management platforms that capture and share tribal knowledge across the organization
- Internet of Things (IoT) sensors that give workers real-time visibility into equipment performance and process variables
- Augmented Reality (AR) tools providing hands-free, context-aware visual guidance for complex assembly or maintenance tasks
By reducing time spent searching for information, digitizing workflows and improving task precision, these technologies transform manufacturing workers from task executors into active participants in operational excellence.
Redesigning Work for Knowledge Transfer
Beyond technology, the smart labor approach to manufacturing involves fundamentally rethinking how manufacturing work is organized to facilitate knowledge development and transfer. Traditional manufacturing job designs often created knowledge silos, with expertise concentrated in a few long-tenured individuals. The new approach aims to distribute knowledge more broadly and transfer it more effectively.
Several innovative work design strategies are emerging to enable this.
Modular Job Design
Some companies are breaking down complex manufacturing roles into more modular components that can be learned more quickly. Rather than requiring years to master all aspects of a position, new workers can become productive in specific modules while gradually expanding their expertise.
Take the example of an aerospace manufacturer that decides to reorganize its composite fabrication process into distinct skill modules. New employees can now become proficient in basic layup techniques within weeks, while more complex skills like troubleshooting cure cycle issues can be taught progressively. This approach allowed the company to integrate new workers more quickly while still preserving a path to deep expertise.
Structured Mentorship Programs
Formal mentorship programs are being implemented to ensure direct knowledge transfer between experienced and newer workers. Unlike casual on-the-job training, these programs include structured activities, documentation requirements, and dedicated time allocations.
Mentoring programs within manufacturing and industrial sectors are a powerful way to reduce injuries, increase productivity and retention, and improve employee satisfaction. Many heavy equipment manufacturers are implementing knowledge transfer programs to capture the expertise of retiring workers. These programs often involve pairing experienced workers with newer employees for mentoring, documenting troubleshooting scenarios, and collaborative problem-solving. By systematically transferring knowledge, companies can mitigate the risk of losing critical expertise and maintain operational effectiveness.
Cross-Training and Rotation Programs
Cross-training workers across different roles and rotating them through various positions helps spread knowledge throughout the organization while creating a more flexible workforce.
Imagine the example of a medical device manufacturer implementing a rotation program where production team members spent time in quality assurance, process engineering, and customer support roles. This not only distributes expertise more widely but gives workers a more comprehensive understanding of how their work affects the entire value chain. This will help ensure fewer quality issues and more proactive problem-solving on the production floor.
Communities of Practice
Formal and informal communities of practice bring together workers with similar roles or interests to share knowledge, solve problems, and develop best practices.
Precision machining companies are increasingly recognizing the value of knowledge sharing among operators. Initiatives such as regular meetings or communities of practice allow machinists from different shifts and product lines to share techniques, troubleshooting approaches, and process improvements. These efforts can lead to reduced setup times and lower scrap rates, contributing to improved efficiency and profitability.
Developing the Manufacturing Talent Pipeline
While redesigning work and deploying technology can make existing workers more effective, the long-term success of American manufacturing depends on developing a pipeline of new talent suited to this smart labor paradigm. This requires rethinking how we attract, train, and develop manufacturing workers.
Rebranding Manufacturing Careers
The first challenge we face is perceptual. For too long, manufacturing has been portrayed as a declining industry offering primarily low-skilled, repetitive work. This perception has steered many talented young people away from manufacturing careers, a trend I've witnessed firsthand throughout my career and one that drove me to found Dirac.
At Dirac, we're not just building cutting-edge manufacturing software; we're on a mission to revitalize American manufacturing by making manufacturing careers exciting and meaningful again. When I speak with manufacturing leaders across the country, I consistently hear the same concern: "How do we attract the next generation of talent?" The answer lies in transforming not just how we talk about manufacturing, but fundamentally changing what manufacturing work entails.
Industry initiatives like Manufacturing Day, where companies open their facilities to students and community members, help showcase modern manufacturing environments. But showcasing isn't enough, we need to create environments worth showcasing. That's where our technology comes in.
Our BuildOS platform, the world's first automated work instruction platform, transforms the manufacturing experience by converting traditional paper-based instructions into interactive, digital formats with 3D animations. I've seen firsthand how this technology shift changes how workers interact with production processes, moving them from manual, repetitive tasks to knowledge-based roles that require digital literacy and critical thinking.
When young people see manufacturing as a pathway to apply creativity, technical skills and problem-solving in meaningful ways, we'll begin to reverse the talent drain that has challenged this sector for decades.
Reimagining Manufacturing Education
Traditional manufacturing education often focused on specific technical skills with limited attention to problem-solving, continuous improvement, and technology adaptation. The smart labor approach requires a more holistic educational model.
Progressive manufacturing education programs now combine:
- Technical foundations in relevant disciplines like machining, electronics, or materials science
- Digital literacy including data analysis, computer-aided design, and manufacturing software
- Problem-solving methodologies such as Six Sigma, lean manufacturing, and design thinking
- Collaboration and communication skills essential for team-based manufacturing environments
- Continuous learning mindsets that prepare workers for ongoing adaptation and growth
Community colleges are often at the forefront of this evolution. Institutions like Greenville Technical College in South Carolina have created advanced manufacturing programs that combine hands-on technical training with exposure to Industry 4.0 technologies and improvement methodologies. These programs produce graduates who are not just technically proficient but prepared to contribute to continuous improvement and innovation.
Accelerated Skill Development
Traditional manufacturing career paths often required years of experience before workers could take on complex responsibilities. In today's fast-changing environment, companies need approaches that accelerate skill development without sacrificing quality.
Automotive manufacturers are increasingly adopting VR-based training for complex assembly operations, leading to improved efficiency and enhanced skills development. The simulations allowed trainees to practice the same operation dozens of times with immediate feedback, accelerating the development of muscle memory and procedural knowledge.
Continuous Learning Infrastructure
Perhaps most importantly, smart manufacturing requires an infrastructure for continuous learning throughout workers' careers. As technologies and processes evolve, workers need ongoing opportunities to develop new skills and knowledge.
Progressive manufacturers are creating internal "learning ecosystems" that include:
- Microlearning modules that deliver targeted training in short, accessible formats
- Peer learning networks that facilitate knowledge sharing among workers
- Career pathways that clearly map skill development to advancement opportunities
- Learning time allocations that dedicate a percentage of work hours to skill development
- Credentialing systems that recognize and reward new skill acquisition
These learning ecosystems recognize that in smart manufacturing, workforce development isn't a one-time event but an ongoing process integral to the business.
The Economics of Smart Labor in Manufacturing
The smart labor approach requires investment in technology, training, work redesign, and knowledge management. For companies accustomed to minimizing labor costs, these investments may initially seem counterintuitive. However, the economics of smart labor are compelling when viewed holistically.
Consider the following value drivers:
- Productivity amplification: Smart labor approaches typically deliver productivity improvements of 25-40% per worker, allowing companies to produce more with fewer people. Smart factory initiatives have shown projected improvements in manufacturing throughput between 10 and 15 percent.
- Quality improvements: Better-trained, technology-enabled workers produce fewer defects, reducing scrap, rework, and warranty costs.
- Innovation acceleration: Workers who understand both the technical and practical aspects of production can contribute valuable insights to product and process innovation.
- Flexibility and responsiveness: A knowledgeable, versatile workforce can adapt more quickly to changing product requirements or market demands.
- Reduced knowledge loss risk: Systematic knowledge capture and transfer reduces the operational risk associated with worker retirements or departures.
Studies have shown that manufacturers implementing technology-enabled workforce development programs can achieve a significant return on investment through quality improvements and productivity gains. Adapting off-the-shelf analytic tools can yield a median ROI of 140% compared to custom-developed solutions. This creates economic space for higher wages, which in turn helps attract and retain talent. Rather than competing in a race to the bottom on labor costs, companies can compete in a race to the top on labor value.
Amplify Worker Productivity with BuildOS's Smart Labor Tools
From day one, BuildOS was designed to transform your operators from task executors into knowledge workers and problem solvers across your manufacturing operation.
BuildOS empowers every operator to become more productive, precise, and innovative thanks to our suite of tools including:
- Automated Work Instruction Generation: BuildOS reduces the time to create work instructions by up to 95%, allowing engineers to focus on innovation rather than paperwork.
- Real-Time Knowledge Access: Workers gain instant access to the tribal knowledge and expertise of your organization, eliminating time wasted searching for information or repeating past mistakes.
- Modern Digital Interface: BuildOS's intuitive digital interface brings manufacturing documentation into the 21st century.
Ready to amplify your manufacturing workforce's productivity? Schedule a demo to discover how BuildOS can help you transition a smart labor approach in your manufacturing operation.
Empowering American Talent to Drive a Smart Manufacturing Future
The shift from cheap labor to smart labor represents more than just a change in workforce strategy, it's a fundamental reimagining of American manufacturing's competitive position in the global economy. Rather than attempting to match the labor cost advantages of developing economies (a battle that cannot be won), the smart labor approach leverages America's strengths in innovation, education, and technology to create a different kind of advantage.
This approach aligns with broader economic and technological trends. As automation continues to advance, the purely manual aspects of manufacturing will represent a shrinking proportion of total production costs. The real value will increasingly come from the knowledge work surrounding production: the process improvements, problem-solving, innovation, and quality management that determine whether a manufacturing operation succeeds or fails.
For individual workers, the smart labor paradigm offers a more promising future than the traditional manufacturing model. Rather than competing against ever-lower global wages or inevitable automation, workers can develop high-value skills that complement technology. These skills command higher wages and offer greater job security, as they are both more valuable to employers and less susceptible to either offshoring or automation.
For communities, smart manufacturing offers a path to rebuild a manufacturing base that provides good jobs and economic stability. While these operations may employ fewer people than the factories of the past, they create higher-value jobs with better wages and career paths. They also tend to support an ecosystem of related knowledge work in design, engineering, and supply chain management.
The transition to smart manufacturing won't happen automatically. It requires intentional investment from companies, supportive policies from the government, and innovative approaches from educational institutions. Most importantly, it requires a shift in mindset, from seeing workers primarily as a cost to recognizing them as a source of value and competitive advantage.
The manufacturers that embrace this shift will be the ones that thrive in the coming decades. They'll build operations that are not just cost-competitive but knowledge-competitive, factories powered not by the cheapest labor, but by the smartest workforce. In doing so, they'll write the next chapter in American manufacturing: a renaissance built not on the past model of mass employment, but on a new model of high-value, knowledge-intensive production that plays to America's unique strengths.
This article is the third in a four-part series examining the manufacturing knowledge crisis and its solutions. Next in the series: "The Ticking Clock: Capturing Your Factory's Tribal Knowledge Before It's Gone Forever"

Dirac is the Assembly Company of the future.
350 5th Ave Ste 4720, New York, New York