The Ticking Clock: Capturing Your Factory's Tribal Knowledge Before It's Gone Forever
How Smart Technologies Are Capturing Critical Manufacturing Expertise Before It's Lost Forever
June 30, 2025
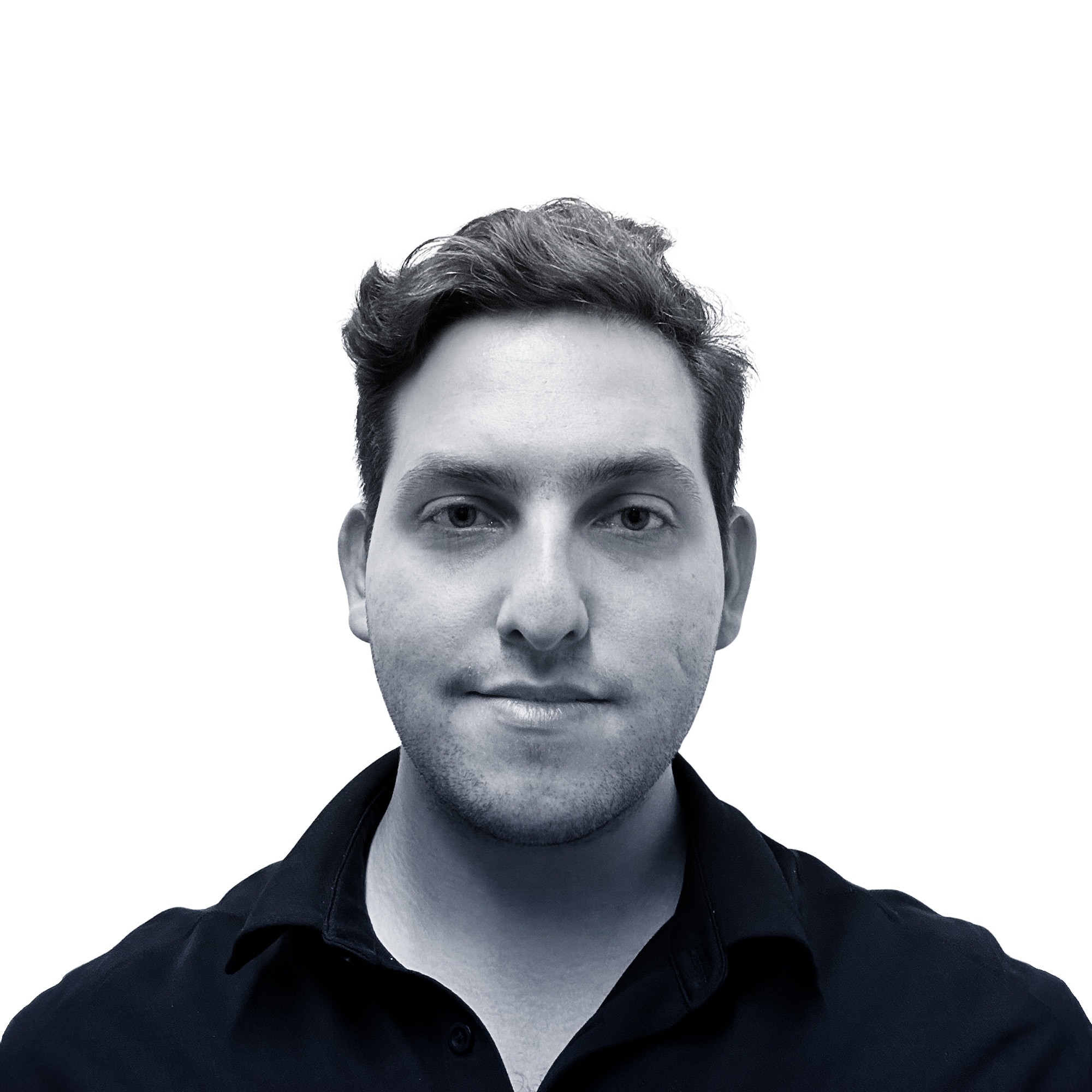
The manufacturing floor holds decades of wisdom. Every experienced operator, maintenance technician and process engineer carries invaluable “tribal knowledge” that can't be found in any manual. Yet as the manufacturing workforce ages and skilled workers retire at unprecedented rates, this critical manufacturing expertise walks out the door forever, taking with it the subtle insights, troubleshooting techniques, and process optimizations that keep production lines running smoothly.
The numbers tell a stark story: nearly one-quarter of U.S. manufacturing workers are 55 or older. A recent survey found that 97% of manufacturers express significant concern about the "brain drain" of retiring workers. Looking into the future, the U.S. manufacturing sector faces an even more daunting challenge, the need to fill about 3.8 million new jobs by 2033, with nearly 1.9 million expected to go unfilled due to skill gaps and retirements.
This knowledge drain in American manufacturing represents one of the most pressing challenges facing modern manufacturers. The gap between what's documented and what experienced workers actually know creates vulnerability that threatens operational continuity, quality standards and competitive advantage.
However, forward-thinking manufacturers are deploying an array of digital tools specifically designed to capture, preserve and distribute tribal knowledge. These technologies don't just document what workers know, they transform that knowledge into accessible, actionable formats that can guide less experienced employees and even enhance the capabilities of veterans. They are, in essence, digitizing the factory brain.
Key Takeaways
- The crisis is immediate and costly: Nearly 25% of U.S. manufacturing workers are 55 or older, with 70% of critical undocumented knowledge at risk of being lost forever as they retire.
- Financial impact is massive: Human error-related downtime costs U.S. manufacturers $92 billion annually, while each skilled worker replacement costs $20,000 to $40,000.
- Traditional documentation fails: Manufacturing expertise is sensory, contextual, and often unconscious, making it impossible to capture through standard manuals or basic training videos.
- Digital solutions are transforming knowledge capture: Digital Work Instructions, digital twins and connected worker platforms can preserve tribal knowledge in real-time, actionable formats.
- Integration beats isolation: The most effective knowledge systems embed expertise directly into daily workflows through digital work instructions and existing manufacturing systems rather than creating separate repositories.
- Culture drives success: Engaging experienced workers as partners and addressing knowledge hoarding concerns is more critical than the technology itself for successful implementation.
- Start with high-impact areas: Focus first on documenting knowledge for critical equipment troubleshooting, complex process setups, and specialized maintenance to demonstrate quick wins and build organizational support.
The Costs of Tribal Knowledge Loss in Manufacturing
Manufacturing organizations today face a perfect storm of knowledge loss. Retirements account for 82% of recent workforce attrition, with the majority of leavers retiring due to age or health reasons according to the National Association of Manufacturers. This isn't just about losing personnel, it's about losing the institutional memory that enables efficient operations.
The financial impact is staggering. Today the cost of one hour of downtime ranges from $39,000 up to $2 million in some facilities. Even a 20% increase in downtime could cause $20-50 million in annual losses for companies with $1 billion in revenue.
Notably 23% of machine downtime is caused by human errors, resulting in an estimated $92 billion annual loss for U.S. manufacturers. Even worse, up to 70% of critical undocumented knowledge may be lost with retiring engineers. Each time a skilled worker is lost to retirement or turnover, manufacturers incur replacement costs of $20,000 to $40,000, and 62% of companies report turnover is getting worse.
Operational inefficiencies compound the problem: a Siemens report found that recovery time from downtime has increased by 60% over the past five years. With less experienced workers struggling to diagnose and fix complex machinery, downtime and safety risks rise, while lost business opportunities and market competitiveness further erode profitability.
Without proactive measures to capture and transfer institutional knowledge, manufacturers face not only higher costs and lower productivity but also a continued decline in operational efficiency and resilience.
Why Manufacturing Expertise Is So Hard to Document
Manufacturing expertise has several characteristics that make it particularly challenging to document:
- It's sensory and tactile: Experienced workers often rely on what they see, hear, and feel, the sound of a machine running correctly, the feel of a proper weld, the visual cues of material behavior. These sensory aspects are difficult to convey in writing.
- It's contextual: Manufacturing knowledge is highly situation-dependent. A solution that works under one set of conditions may not apply under slightly different circumstances. This contextual nature makes it difficult to create comprehensive documentation.
- It's often unconscious: Veteran workers frequently don't realize the extent of their specialized knowledge because it has become second nature to them. They may not even recognize that they're making adjustments or decisions that others wouldn't know to make.
- It's constantly evolving: Manufacturing knowledge isn't static. It evolves as materials, equipment, and processes change. Documentation quickly becomes outdated unless continuously maintained.
- It crosses disciplinary boundaries: Manufacturing expertise often spans multiple domains, mechanical, electrical, materials science, quality systems, and more. This interdisciplinary nature makes it difficult for any single documentation approach to capture the full picture.
These characteristics help explain why traditional knowledge management approaches often fall short in manufacturing environments. Three-ring binders of procedures, basic training videos, or standard work instructions simply cannot capture the rich, multidimensional nature of manufacturing expertise.
Digital technologies, however, offer new possibilities. They can capture multiple dimensions of knowledge simultaneously, incorporate context, update dynamically, and present information in formats that match how humans actually learn and work.
Effectively Integrating Manufacturing Knowledge into Workflows
Capturing knowledge is only the first step. For digital knowledge systems to be effective, they must be integrated into daily workflows where they can guide decisions and actions in real-time. This integration transforms static documentation into living knowledge systems that drive operational excellence.
Structured Documentation Techniques
Structured Documentation Techniques provide a systematic approach to capturing and organizing manufacturing knowledge to ensure consistency, clarity, and ease of retrieval. These techniques include the use of standardized templates, step-by-step guides, process flowcharts, and digital manuals that are regularly updated and collaboratively maintained.
By employing structured documentation, manufacturers can reduce ambiguity and variation in work processes, making it easier for employees to follow best practices and for organizations to preserve critical tribal knowledge. Workshops, interviews, and continuous feedback loops help keep documentation relevant and comprehensive.
When combined with digital tools like knowledge management systems and connected worker platforms, structured documentation becomes a powerful enabler of operational excellence and workforce development.
However, template-based approaches to knowledge documentation present significant limitations for long-term knowledge preservation in manufacturing environments. Templates inherently struggle to capture the dynamic, multidimensional nature of manufacturing expertise. The rigid structure of templates forces complex, contextual knowledge into predetermined formats that often strip away critical nuances and tacit understanding that experienced operators possess. What appears comprehensive on paper frequently lacks the depth needed for real-world application.
Digital Work Instructions
Digital work instructions (also known as electronic work instructions) are virtual versions of traditionally paper-based instructions and manuals that are accessible on electronic devices. Digital work instructions are created and managed by purpose-built work instructions software designed specifically for manufacturing. Unlike their physical counterparts, digital work instructions offer much more than just text on a screen, they represent a complete paradigm shift in how information is delivered, consumed, and utilized on the manufacturing floor.
At their core, digital work instructions transform static printed documents into dynamic, interactive tools that guide workers through complex processes. They provide real-time, step-by-step directions complete with visual aids and contextual information on the best way to complete a task. These digitized instructions and work procedures are kept in a centralized system so workers can easily access them to work on tasks or make decisions on projects.
The benefits are substantial: improved workforce productivity, increased quality, and accelerated training. Digital work instructions help manufacturers reduce errors, preserve critical knowledge and avoid costly disruptions on the shop floor.
Digital Twins for Knowledge Documentation
Digital twins are revolutionizing how manufacturers document and utilize operational knowledge. A digital twin is a real-time, virtual replica of a physical asset, process, or system that continuously collects and organizes data from sensors and connected devices on the shop floor. This technology offers a centralized, structured record of how equipment and processes perform under various conditions, capturing not only raw data but also the nuanced adjustments and best practices developed by experienced workers.
By embedding expert insights and process knowledge directly into the digital model, digital twins make it possible to preserve critical tribal knowledge that might otherwise be lost as employees retire or move on. These virtual environments also support immersive training and onboarding, allowing new hires to interact with simulated equipment and scenarios that reflect real-world operations. As processes evolve, digital twins enable teams to annotate changes, attach supporting documentation, and update best practices in real-time, ensuring that knowledge remains current and actionable.
Integrating digital twins with knowledge management systems and connected worker platforms creates a living repository of expertise that drives continuous improvement, reduces downtime, and empowers teams to make informed decisions based on the best available information. This approach not only safeguards institutional knowledge but also accelerates innovation and operational excellence across the manufacturing enterprise.
Knowledge Management Systems
Knowledge Management Systems (KMS) are foundational tools for capturing, organizing, and sharing tribal knowledge within manufacturing organizations. Leading platforms like Confluence, Notion, SharePoint, and Guru centralize critical information, making it accessible and actionable across teams. These systems support collaborative documentation, version control, and seamless integration with other enterprise tools such as ERP and MES, ensuring knowledge remains current and embedded in daily workflows.
Advanced KMS solutions now incorporate AI-driven search and recommendation engines, enabling workers to quickly find relevant expertise and best practices. By transforming static documents into dynamic knowledge hubs, KMS platforms help manufacturers reduce knowledge silos, accelerate onboarding, and improve operational consistency.
Integrating KMS with digital work instructions and connected worker platforms further enhances real-time decision-making and continuous improvement on the shop floor.
Connected Worker Platforms
Connected Worker Platforms are specialized digital solutions designed to capture and leverage tribal knowledge directly from the shop floor in real-time. These platforms empower operators and technicians to document issues, solutions, and best practices as they occur, creating a living repository of actionable knowledge.
Examples like 4Industry enable seamless communication between workers and management, facilitating rapid problem resolution and continuous process improvement. By integrating with manufacturing execution systems (MES) and digital work instructions, connected worker platforms transform tribal knowledge into standardized operating procedures, work instructions, and one-point lessons.
The real-time nature of these platforms ensures that knowledge is always up-to-date and contextually relevant, helping manufacturers reduce downtime, improve quality, and accelerate training.
Building A Culture of Documenting Manufacturing Knowledge
While digital knowledge technologies offer powerful capabilities, implementing them successfully requires thoughtful planning and change management. Companies that have successfully digitized tribal knowledge typically follow several best practices:
Start with Critical Knowledge Areas
Rather than attempting to digitize all knowledge at once, successful implementations focus first on the most critical areas where knowledge loss would have the greatest impact. This might include:
- Troubleshooting for critical equipment
- Setup and optimization of complex processes
- Quality inspection for difficult-to-detect issues
- Maintenance of specialized machinery
- Process adjustments for challenging materials or conditions
By prioritizing these high-value areas, companies can demonstrate quick wins that build support for broader implementation.
Engage Experienced Workers as Partners
Digital knowledge capture works best when experienced workers are engaged as active partners rather than passive subjects. This means:
- Explaining how their expertise will benefit the organization even after they retire
- Involving them in decisions about what knowledge to capture and how
- Recognizing and rewarding their contributions to knowledge preservation
- Addressing concerns about job security or being "replaced"
Companies that position knowledge capture as honoring and preserving veterans' legacies typically see much higher engagement than those that present it as simply extracting information.
Integrate with Existing Systems and Workflows
Knowledge technologies should integrate seamlessly with existing systems rather than creating separate repositories that workers must consult. This might involve:
- Embedding knowledge in digital work instructions
- Integrating video libraries with equipment via QR codes
- Connecting knowledge platforms to MES and ERP systems
- Making knowledge accessible through familiar interfaces
The goal is to make knowledge available within the flow of work, not as a separate activity.
Address Cultural Barriers
Cultural factors often present the biggest challenges to knowledge digitization. Common barriers include:
- Knowledge hoarding as job security
- Skepticism about the value of documentation
- Resistance to changing established ways of working
- Concerns about being monitored or evaluated
Successful implementations address these barriers through clear communication, appropriate incentives, and visible leadership support.
Plan for Continuous Evolution
Digital knowledge systems should be designed to evolve over time rather than capturing knowledge as a one-time event. This means:
- Building in mechanisms for updating and refining captured knowledge
- Establishing processes for validating and approving knowledge contributions
- Creating roles responsible for knowledge curation and management
- Measuring and reporting on knowledge system usage and impact
The most effective knowledge systems grow more valuable over time as they incorporate new insights and adapt to changing conditions.
Preserve Your Manufacturing Expertise with BuildOS
Every manufacturer faces the same ticking clock: experienced operators with decades of irreplaceable knowledge are approaching retirement. When they leave, they take with them the countless unwritten rules, techniques and insights that make your manufacturing processes work.
BuildOS provides a structured framework to capture and preserve this tribal knowledge before it walks out the door. Our platform:
- Automatically generates work instructions directly from your CAD files
- Provides intuitive tools for your operators to document their tribal knowledge
- Embeds your tribal knowledge directly into your assembly sequences
- Creates a permanent, accessible record of your team’s manufacturing expertise and tribal knowledge
This isn't just documentation, it's knowledge preservation. The specialized knowledge that took decades to develop becomes a permanent asset of your organization, accessible to new generations of workers through clear, visual instructions.
Schedule a demo to learn more about how BuildOS can help you preserve and transfer critical expertise before it's too late.
Building America's Manufacturing Memory: The Path Forward
The digitization of manufacturing knowledge represents more than just a technological solution to the retirement wave, it's a fundamental shift in how we think about expertise in industrial settings. Rather than treating knowledge as something that exists primarily in individual minds, digital approaches recognize knowledge as an organizational asset that can be captured, preserved, and deployed strategically.
This shift has profound implications. It means that the expertise developed over decades doesn't have to walk out the door when workers retire. It means that new employees can access the insights of veterans they never met. It means that knowledge developed in one facility can benefit operations around the world. And it means that manufacturing organizations can become truly learning enterprises, where knowledge accumulates and improves over time rather than being constantly lost and rediscovered.
For individual manufacturers, the imperative is clear: begin digitizing critical knowledge now, before it's lost. The technologies exist. The methodologies are proven. The return on investment is compelling. What's required is the organizational will to make knowledge preservation a strategic priority.
For the manufacturing sector as a whole, widespread adoption of digital knowledge technologies could help reverse the erosion of industrial expertise that has accompanied decades of offshoring and underinvestment in workforce development. By preserving the deep knowledge of today's experts and making it accessible to the next generation of manufacturing workers, we can rebuild the foundation of manufacturing excellence that once defined American industry.
The factories of the future will compete not just on equipment, materials or labor costs, but on their ability to capture, preserve, and deploy knowledge effectively. Those that build robust digital knowledge infrastructures today will have a decisive advantage in that competition. They will, in essence, be building not just physical production capacity, but a manufacturing memory bank that will pay dividends for decades to come.
This article is the final installment in a four-part series examining the manufacturing knowledge crisis and its solutions.
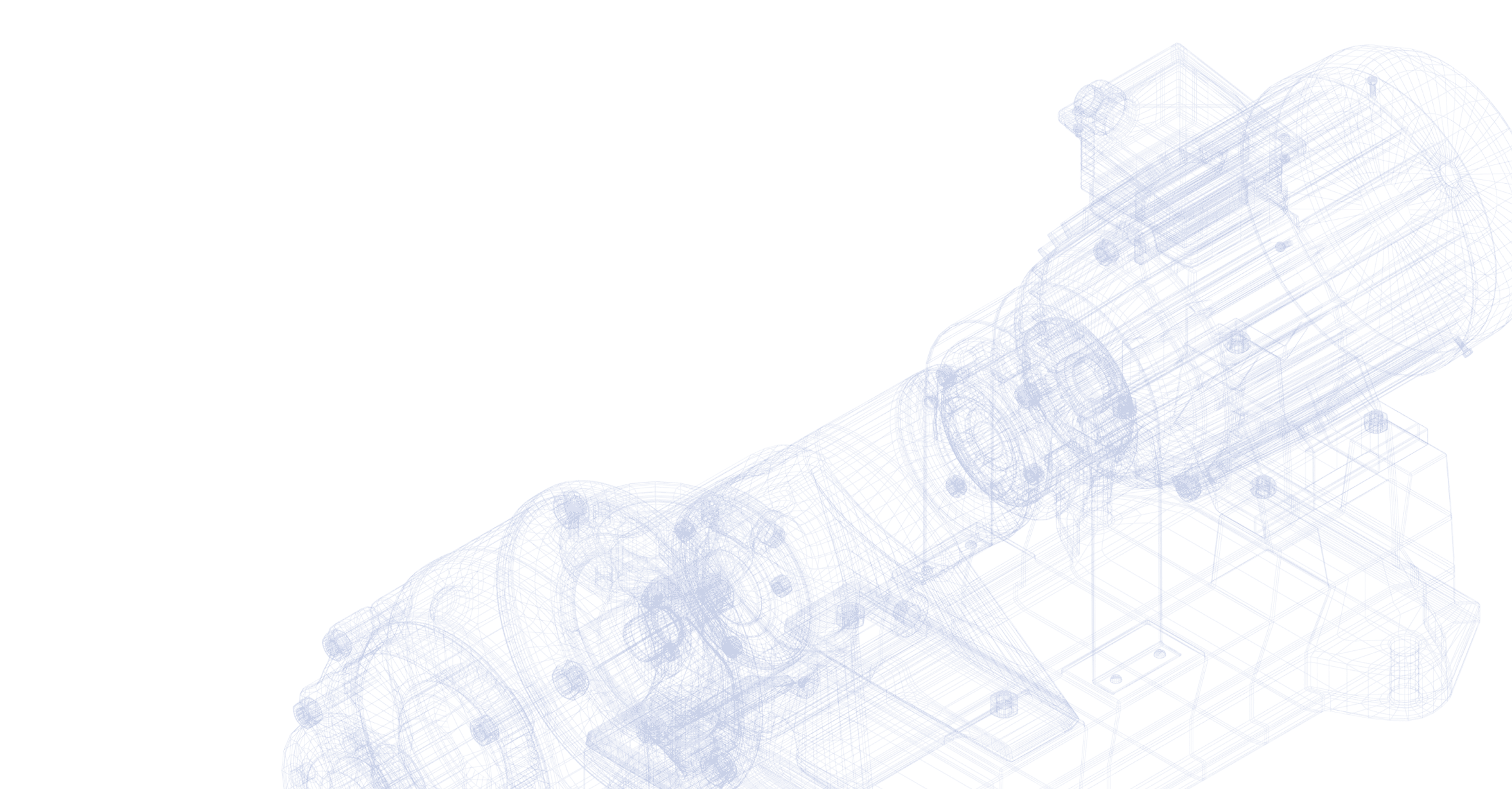
Dirac is the Assembly Company of the future.
350 5th Ave Ste 4720, New York, New York