What is a Work Instruction?
Everything You Need to Know About Work Instructions And Why They Are a Vital For Manufacturing
July 22, 2025
The manufacturing skills gap is widening at an alarming rate. With nearly 600,000 unfilled U.S. manufacturing jobs in 2023 and projections showing 2.1 million unfilled positions by 2030, manufacturers face a critical challenge: how do you maintain operational excellence when institutional knowledge walks out the door with retiring workers? Add to this the fact that 2.7 million baby boomers are retiring this year, and the urgency becomes clear.
When critical assembly processes fail because operators follow different procedures, or when quality issues arise from unclear task guidance, the financial impact is severe. Rework and scrap can consume 20-50% of project costs, while manufacturing defects typically represent 12.5% of product sales. In this high-stakes environment, a well-crafted work instruction serves as the foundation for operational excellence, ensuring every task is performed correctly, safely, and efficiently regardless of who's on the floor.
The solution is clear: manufacturers who implement comprehensive standardized work processes see a 6.5% increase in process productivity, while systematic SOPs reduce training time by 65% and decrease defect rates by 40%. Yet many organizations struggle with creating work instructions that actually work in practice, often ending up with documents that gather dust rather than drive results.
What is a Work Instruction?
At a high-level a work instruction is a detailed, step-by-step document that provides precise directions for completing a specific task within a manufacturing process. Unlike broader standard operating procedures (SOPs), work instructions focus on the granular "how-to" details that ensure consistent execution at the operator level.
A work instruction encompasses several key characteristics:
- Task-specific guidance that breaks down complex processes into manageable steps
- Visual aids and diagrams that support written directions
- Safety protocols integrated throughout the procedure
- Quality checkpoints that prevent defects from moving downstream
- Clear prerequisites including required tools, materials, and skills
Think of work instructions as the GPS navigation system for your manufacturing floor. Just as GPS provides turn-by-turn directions to reach a destination, work instructions guide operators through each action required to complete a task successfully.
The market clearly recognizes this value. The work instruction software market is projected to exceed $3.7 billion by 2033, reflecting the growing recognition that software is a critical enabler for work instruction creation, effective documentation and operational success for manufacturers.
The Critical Role of Work Instructions in Modern Manufacturing
Manufacturing environments are evolving at an unprecedented pace. With increasing product variations, stricter regulatory requirements, and a growing need to rapidly onboard new employees, the complexity of today’s shop floors has never been higher. In this context, work instructions have emerged as a linchpin for operational excellence. Let’s explore the multifaceted benefits and the expanding role of work instructions in modern manufacturing.
Error Prevention and Quality Assurance
Work instructions act as guardrails against human error, a leading cause of unplanned downtime and defects. Research shows that clear visual instructions can improve learning retention by up to 400% compared to text-only guides. When operators follow well-designed, visual instructions, misinterpretations are minimized, and costly mistakes are reduced. This systematic approach is crucial, as approximately 23% of unplanned downtime in manufacturing is attributed to human error.
But how do work instructions achieve this? By breaking down complex processes into simple, actionable steps, they ensure that every employee, regardless of experience, performs tasks consistently and correctly. This not only reduces errors but also enhances the overall quality of the final product. In fact, companies that implement standardized work instructions report up to 20% fewer defects and significantly improved first-pass yields.
Training and Knowledge Transfer
Labor shortages continue to challenge manufacturing firms, with 30% reporting production constraints due to staffing issues. In this environment, effective knowledge transfer becomes mission-critical. Work instructions serve as vital knowledge repositories, capturing institutional know-how that might otherwise be lost when employees retire or move on.
Digital and visual work instructions are especially powerful tools for training. They break down complex tasks into digestible visuals, reducing cognitive load and accelerating the learning process. Some organizations have reported up to 50% faster training times with digital work instructions, enabling new hires to become productive more quickly. This not only addresses labor shortages but also ensures that best practices are consistently applied across the organization.
Preserving Tribal Knowledge and Supporting Succession
Manufacturing faces a critical knowledge exodus, nearly 25% of workers are 55+ and 97% of manufacturers worry about this "brain drain." This demographic shift threatens to erase operational expertise that exists only in experienced workers' minds.
High-quality work instructions can capture this institutional know-how before it vanishes. By documenting specialized techniques, troubleshooting methods and process optimizations, they transform individual expertise into permanent organizational assets.
The financial impact is clear: skilled worker replacements cost $20,000-$40,000 each, while human error-related downtime drains $92 billion annually from U.S. manufacturers. Digital work instructions excel at preserving tribal knowledge through multimedia elements that capture nuances text alone cannot convey.
Organizations that systematically document tribal knowledge create sustainable competitive advantage, maintaining operational excellence while accelerating new workforce development.
Regulatory Compliance and Safety
Manufacturing safety remains a top priority, with 391 fatal occupational injuries reported in the sector in 2023 alone. Many industries require documented procedures to meet stringent regulatory standards, such as ISO 9001, IATF 16949, and FDA 21 CFR Part 820. Work instructions provide the detailed documentation needed to demonstrate compliance and support audit activities.
Beyond compliance, work instructions play a critical role in protecting workers. By clearly outlining safety protocols, required personal protective equipment (PPE), and hazard warnings, they help reduce accidents and injuries. OSHA and other regulatory bodies emphasize the importance of written procedures for all safety-critical tasks, making work instructions an essential component of any safety program.
Financial Impact Through Standardization
The financial benefits of standardized work instructions are substantial and far-reaching. Standardizing equipment and processes can reduce supply costs by up to 20%, as employees use the right tools and materials for each task. Additionally, companies with standardized safety protocols experience 53% fewer safety incidents, leading to lower insurance costs and reduced downtime.
Perhaps most compelling is the impact on scrap and rework. These issues can cost manufacturers up to 2.2% of their annual revenue. By minimizing errors and ensuring consistent quality, work instructions help companies avoid these costly pitfalls. The return on investment (ROI) for effective work instructions is clear: reduced waste, lower costs, and improved profitability.
Best Practices for Work Instruction Implementation
Creating great work instructions is only half the battle. Successful implementation requires attention to distribution, training, and continuous improvement, especially in an environment where effective knowledge transfer can make or break operational success.
Make Instructions Digital and Accessible When and Where Needed
The best work instruction is useless if operators can't access it when they need it. Modern manufacturing environments increasingly rely on digital technologies as part of their workflows.
Adopting digital work instructions can help deliver precise, real-time guidance, enhancing task completion speed and reducing errors. Digital work instruction platforms like BuildOS enable real-time access to current procedures, automatic updates, and integration with other manufacturing systems. Digital platforms also support features like animated assembly sequences, video demonstrations, interactive checklists and other features.
Establish Clear Update and Revision Procedures
Manufacturing processes evolve continuously, and work instructions must keep pace. Establish clear procedures for:
- Regular review cycles to ensure instructions remain current and accurate
- Change control processes that prevent unauthorized modifications
- Version control that ensures operators always use the most current instruction
- Feedback mechanisms that allow operators to suggest improvements based on real-world experience
Train Operators on Both Content and Usage
Effective training goes beyond simply reviewing the written instructions. Visual formats promote faster training timelines and inclusivity by making content easier to access and understand. Comprehensive training should include:
- Hands-on Practice: Allow operators to perform the task under supervision while following the work instruction. This reveals gaps between written procedures and actual execution requirements.
- Understanding the Why: Explain the reasoning behind specific steps, particularly safety requirements and quality checkpoints. When operators understand why something is important, they're more likely to follow the instruction consistently.
- Troubleshooting Scenarios: Prepare operators for situations not explicitly covered in the standard procedure. This might include equipment malfunctions, material variations, or unexpected quality issues.
Measuring Work Instruction Effectiveness
To ensure your work instructions deliver expected benefits, establish metrics that track their impact on operational performance:
- Quality Metrics: Monitor defect rates, rework frequency, and customer complaints for processes covered by work instructions. Given that reducing rework by 50% could increase profits by 13%, improvements in these areas often correlate directly with instruction effectiveness and bottom-line impact.
- Training Efficiency: Track how quickly new employees achieve competency on tasks with well-documented work instructions compared to those relying on informal training methods. This becomes especially critical when excessive onboarding times slow workforce scaling and affect consistency.
- Process Consistency: Measure variation in process parameters, cycle times, and output quality across different operators and shifts. Reduced variation typically indicates effective work instruction implementation.
- Safety Performance: Monitor safety incident rates for processes with standardized work instructions. The correlation between clear procedures and safety outcomes provides both moral and financial justification for comprehensive instruction programs.
Common Pitfalls to Avoid
Even well-intentioned work instruction initiatives can fail if they encounter these common obstacles:
- Over-Documentation: Resist the temptation to document every possible scenario or exception. Focus on the core procedure and handle exceptions through separate troubleshooting guides or escalation procedures.
- Insufficient Testing Never deploy work instructions without testing them with actual operators in real conditions. What seems clear to the instruction writer may be confusing to the person performing the task.
- Failing to Update Work Instructions Outdated instructions can be worse than no instructions at all, as they may guide operators toward obsolete or unsafe practices.
- Ignoring Visual Learning Preferences: As we mentioned earlier visual aids can improve learning by up to 400%, yet many organizations still rely solely on text-based instructions. This approach ignores how people actually learn and retain complex procedural information.
Going Digital: The Future of Work Instructions in Manufacturing
As manufacturing continues to evolve, work instructions are becoming more sophisticated and integrated with other systems. Advanced platforms like Dirac’s BuildOS are transforming how manufacturers create, distribute and maintain work instructions by:
- Automatically generates work instructions directly from your CAD files
- Determines the optimal assembly sequence without manual input
- Generates clear 3D renderings and animations for each step
- Produces complete work instruction packages in minutes, not weeks
BuildOS is a purpose-built platform designed to digitize and transform how manufacturing organizations create and manage work instructions. The automation capabilities built into BuildOS aren’t just about speed; they are about consistency. Every work instruction follows the same format, uses the same terminology, and maintains the same quality standards, regardless of which engineer created it or when.
Stop wasting engineering talent on manual documentation. Schedule a BuildOS demo today and see how automation can transform your work instruction process.
Work Instructions Will Always Be Crucial to Manufacturers
Effective work instructions represent a cornerstone of manufacturing excellence, but the window for implementation is narrowing as the skills gap widens. Start by identifying your most critical processes or those with the highest error rates. These represent the best opportunities for immediate impact.
Consider how modern digital platforms can enhance your work instruction effectiveness. BuildOS and similar systems can streamline creation, ensure consistent access, and provide the analytics needed to continuously improve your procedures. The data supports this approach: digital work instructions deliver precise, real-time guidance, enhancing task completion speed and reducing errors.
In an industry where precision and efficiency determine success, there's no substitute for clear, actionable guidance that empowers every operator to perform at their best. The question isn't whether you can afford to implement comprehensive work instruction systems, but whether you can afford not to.
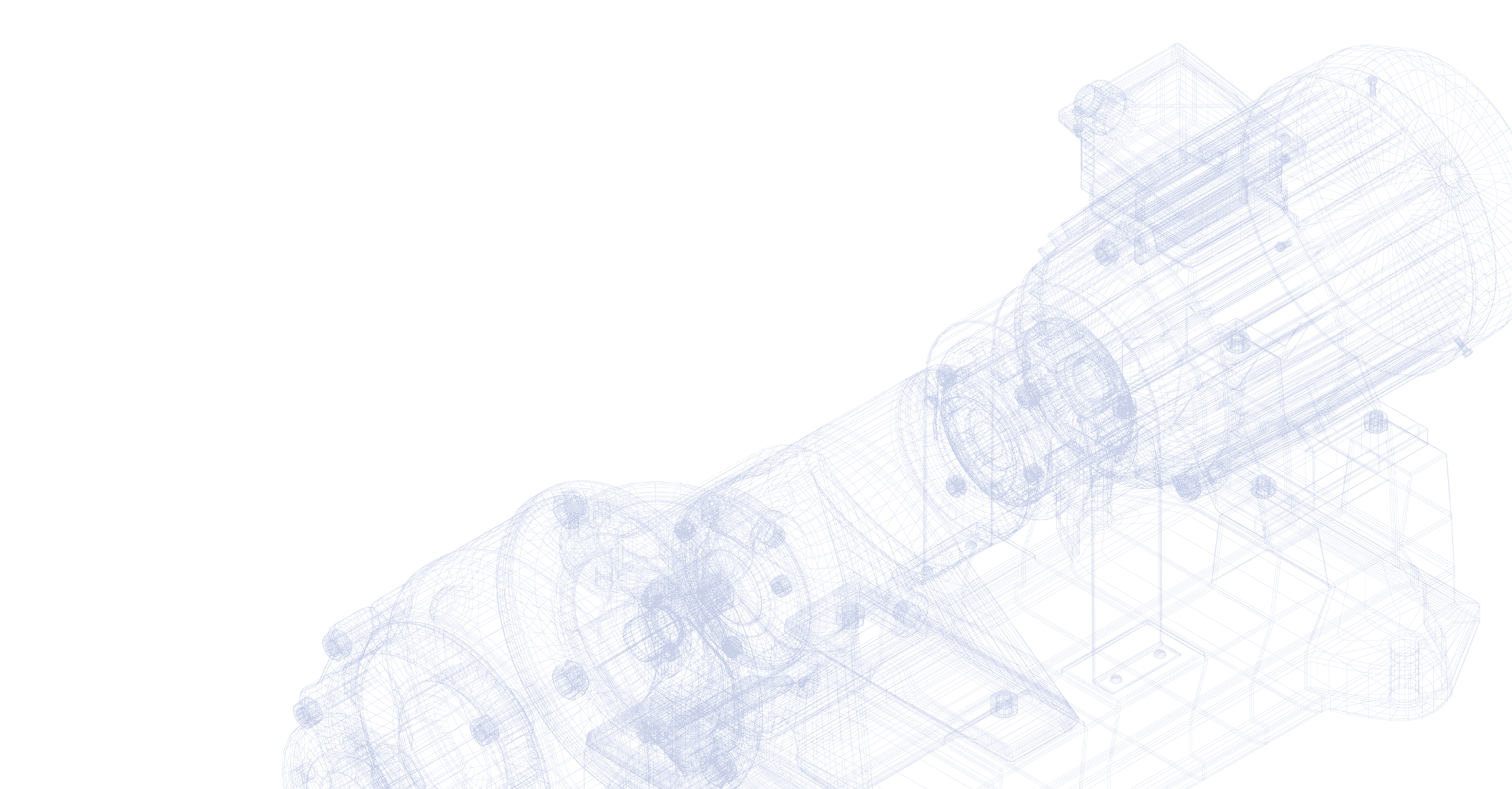
Dirac is the Assembly Company of the future.
350 5th Ave Ste 4720, New York, New York