Answering the Call: Why Technology is Key to Revitalizing US Shipbuilding
Embracing Digitization and Automation to Rebuild US Shipbuilding Power
April 23, 2025
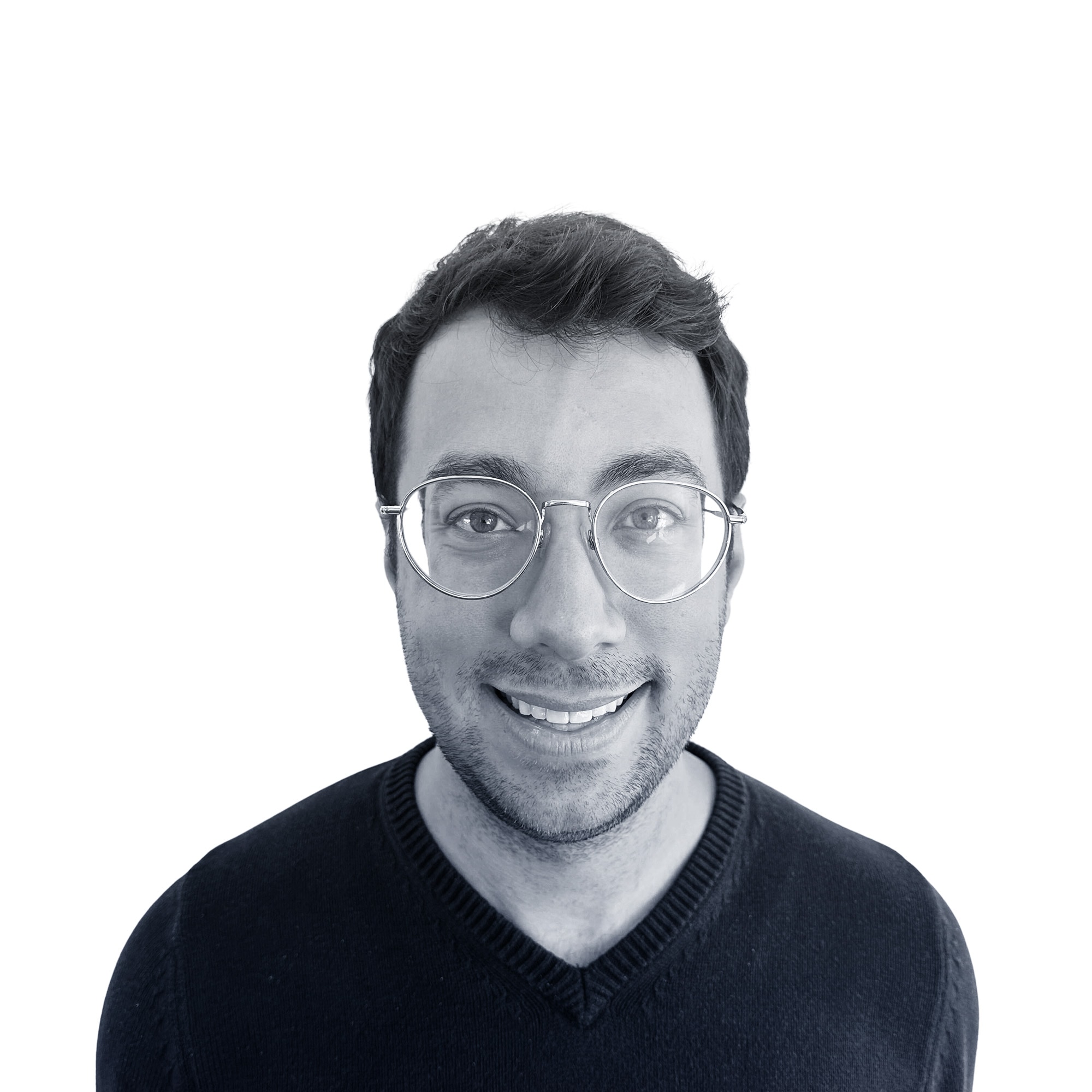
The US shipbuilding industry stands at a critical crossroads. Despite its strategic importance to national security and economic prosperity, the United States only accounts for 0.05% of global shipbuilding output. China on the other hand, produces approximately half of the world's vessels. Recognizing this imbalance, recent executive orders aim to revitalize US shipbuilding capacity and restore maritime superiority.
At the heart of this decline lies a fundamental problem: significant, systemic inefficiencies rooted in outdated processes hinder US shipbuilding capacity, speed, cost-effectiveness, and global competitiveness. The solution, however, is within reach. Modernizing shipyard operations through comprehensive digitization and automation is not only beneficial but necessary to overcome these hurdles and revitalize the American shipbuilding industry. Staying with the out-of-date “business as usual” processes is simply irresponsible.
Inside the Shipyard: Where Things Break Down
The Tyranny of Paper
Walk into most American shipyards today, and you'll encounter mountains of paper: drawings spread across tables, mountains of certification records filed in cabinets, work instructions printed and covered in untracked red-lines, test procedures bound in thick binders, and operational logs written in illegible handwriting. This overwhelming reliance on physical documentation and paper creates a cascade of inefficiencies that destroy productivity.
The consequences are immediate and far-reaching. Workers waste countless hours searching for the right thing, manual verifying and cross-referencing documents, and facing the constant risk of using outdated, incomplete, or misplaced paperwork. The physical storage requirements alone create logistical bottlenecks that almost every other industry abandoned years ago.
Consider a typical scenario: an engineer needs to verify a system was previously built and inspected before testing the system. This seemingly straightforward task requires physically locating and gathering multiple paper records from different departments, who might be out of office. Some of these records might not have sufficient information, requiring you to verify shipboard components before proceeding with the test. What should take minutes in a digital environment can stretch into hours and days in this paper-riddled paradigm.
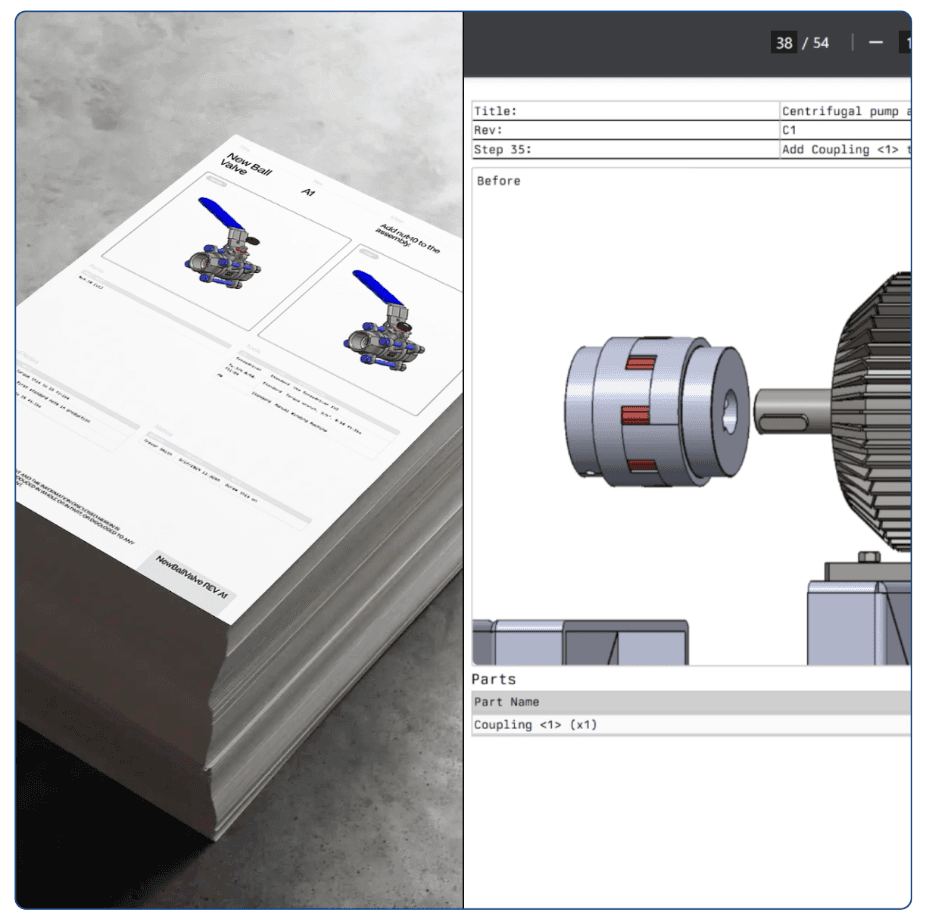
Manual Coordination & The Bottleneck of Tribal Knowledge
Beyond paper, US shipbuilding efficiency is severely hampered by outdated coordination methods. Daily production planning meetings, supervisors negotiating for limited resources, and the constant need to know "who to ask" for specific information all create bottlenecks throughout the shipbuilding process. Furthermore, the lack of a consistent source-of-truth often leaves folks on different pages, and operating with conflicting directives.
Perhaps most concerning is the industry's heavy reliance on "tribal knowledge", critical operational details, undocumented best practices and principles, and process nuances that reside only in the minds of experienced individuals rather than in accessible systems. This creates substantial risks: when personnel leave or retire, crucial knowledge walks out the door with them. New workers face steep learning curves and slow onboarding, while inconsistencies in task performance become inevitable.
Continuing in this vein, high impact production decisions almost always depend on subjective opinions and untraceable feedback.. This manual coordination without any tooling leads to the outcomes we’ve all experienced: getting delayed waiting for that “all clear” phone call to tell you when to go aboard; squeezing down passageways with your gear and finding the space occupied by more urgent work that popped up without your department knowing. Cross-department coordination without the proper tools gives you underperforming departments, a frustrated work force, and increasingly at-risk delivery schedules.
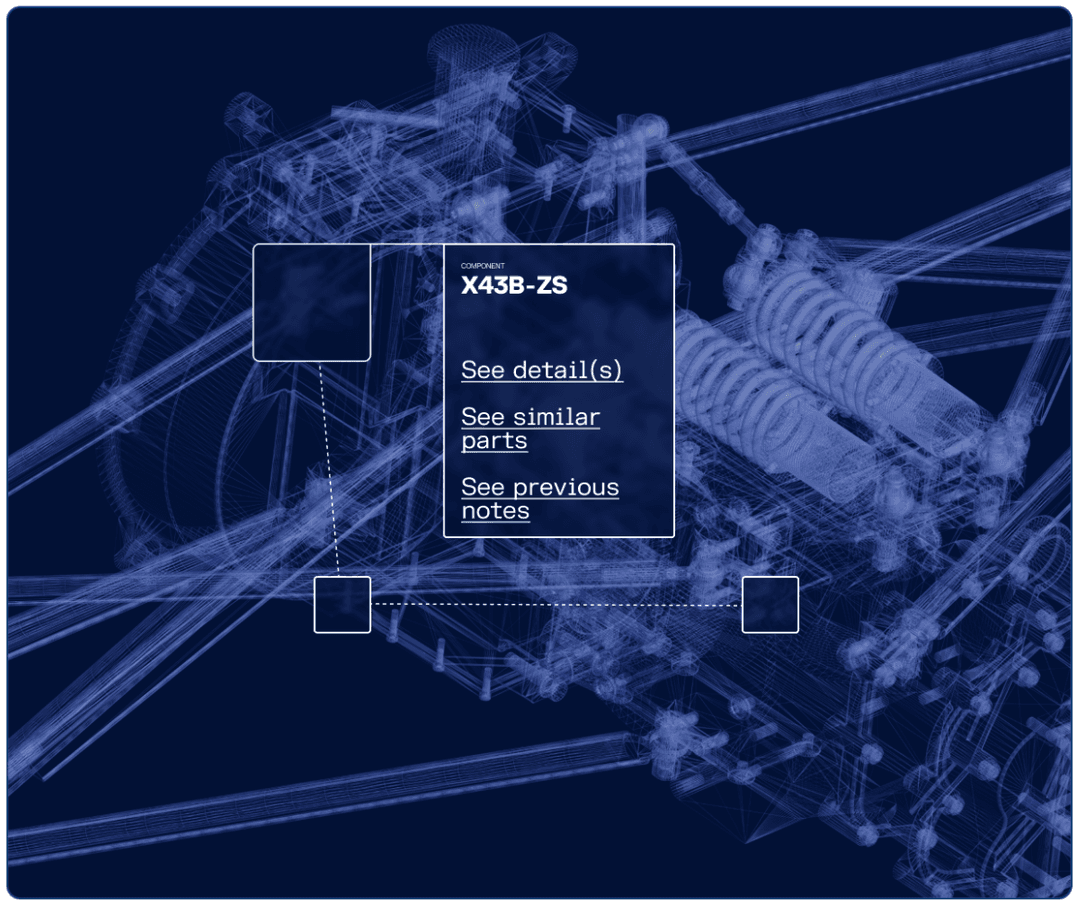
Testing Troubles
The test-driven nature of shipbuilding throws more complexity in the mix. Major construction milestones, like hull closure or system integrations, are typically gated by the successful completion of specific tests. In the vast majority of cases, these tests are non-negotiable requirements.
The test preparation process in traditional shipbuilding environments is cumbersome and manual: teams must gather documented proof that all prerequisite work and inspections are complete, manually create local interpretations of regulated test procedures tailored for a ship's configuration, research past issues documented in scattered paper logs, and manually create briefing materials for test crews.
When this process fails, as it frequently does, the consequences are costly. Teams often discover after test completion that a prerequisite wasn't properly verified, forcing delays, expensive rework, and inefficient reallocation of skilled personnel. The Government Accountability Office found that estimated delays for some naval vessels are as much as 3 years.
Another horror story we’ve all lived through: aligning all shipyard activities for a weekend testing evolution only to find out at the last minute that you cannot perform the test because of missing paperwork. Not only do you have to repeat this song and dance again next weekend after you resolve the issue, you’ve also pushed all the other projects behind a weekend because these preparations are all done manually.Scenarios like this leave you with dollars wasted and schedule slips burning brand equity.
Compliance Challenges & Rework
Shipbuilding quality control demands adherence to stringent standards, particularly so in defense. Meeting these standards consistently using manual, paper-based processes presents challenges that modern digital systems could readily address.
The lack of automated checks forces heavy reliance on manual inspection and human verification, which inevitably results in mistakes. Imagine repeating an entire test procedure because data was recorded with the wrong number of significant digits on a paper form. Such scenarios are unfortunately commonplace in traditional shipbuilding environments and are completely avoidable by adopting digital transformation technologies.
Workforce & Legacy Issues
The challenges facing US shipbuilding extend beyond processes to people. The industry struggles to attract and retain the workforce necessary to build the Navy's future fleet. Key bullet points include an aging workforce, skill gaps, attraction and retention difficulties, and training and upskilling challenges.
This workforce crisis is compounded by the inertia of legacy systems and deeply ingrained and decades-old practices. Compared to other industries like automotive and commercial aerospace, the technology shipyards are using is remarkably unchanged from the early 2000’s.This technology gap and resistance to innovative technology not only impacts efficiency but also makes the industry less attractive to a new generation of workers who want to use digital tools.
The Path Forward: A Vision for Digitally-Driven Shipbuilding
Laying the Digital Foundation: Establishing a Single Source of Truth
The transformation of US shipbuilding begins with establishing a contiguous "digital thread," a centralized digital platform serving as the single source of truth for all manufacturing data. This foundation enables paperless manufacturing and creates a strong foundation upon which other inefficiencies can be identified and addressed.
By digitizing documents, drawings, procedures, certification records, and shipboard logs, critical information becomes instantly accessible, searchable, and auditable. The benefits are immediate: elimination of time-consuming paper chases, drastic reduction in human induced errors, and assurance that everyone works from the same, up-to-date plans and data.
For shipyards, this digital foundation represents the first critical step toward modernization and enhanced competitiveness in the global marketplace.
From Tribal Knowledge to Digital Workflows
Modern manufacturing software for shipyards can capture complex assembly procedures, standard operating practices, and tribal knowledge within structured, digital workflows. This transformation addresses one of the industry's most persistent vulnerabilities.
Interactive, step-by-step digital work instructions augmented with 3D visuals or models, can guide workers of varying experience levels, reducing reliance on specific senior individuals. These instructions can be tied to production milestones, to give you on-demand statuses to help with team prioritization. The result: significantly accelerated training and onboarding, preservation of invaluable operational knowledge within the organization, and consistent, high-quality execution of tasks coordinated across the shipyard.
This shift from tribal knowledge to digital workflows represents a fundamental change in how shipbuilding knowledge is managed and transferred, creating resilience against workforce turnover and enabling more efficient scaling of operations.
Streamlining Testing & Ensuring First-Time Quality
Digital systems can revolutionize the test-driven manufacturing approach that defines shipbuilding. By automatically tracking the real-time status of all prerequisites, these systems provide clear visibility into test-readiness and potential bottlenecks.
Moving data collection off of paper and into the digital environment enforces compliance to acceptance criteria, removing all possibility of entering unsatisfactory values. Ditching the filing cabinets and digitally storing historical data, past issues, and lessons learned provides immediate referenceability during planning and execution.
These benefits are substantial: dramatically reduced preparation time, prevention of costly delays caused by missing or incomplete documentation, and minimized rework stemming from procedural or data errors all support improving overall first-time quality and on-time delivery.
Data-Driven Decisions & Enhanced Traceability
A centralized digital system provides managers and engineers with real-time visibility of production progress, system statuses, and emerging bottlenecks across the shipyard. This enables you to make smarter, data-informed resource allocation and prioritization decisions without any pieces of the puzzle missing.
Equally important is the seamless ability to instantly track any component, assembly, or completed task back through its entire history, including materials and tools used, personnel involved, and an unbroken chain of quality signoffs. This pours jet fuel on your ability to perform root cause and impact analyses while creating robust, easily auditable records for compliance and continuous improvement.
For an industry where quality and compliance are non-negotiable, these technologies represent the desperately needed catalyst to propel shipbuilding into the digital age.
Eliminate Paper, Elevate Performance with BuildOS
Paper-based work instructions aren't just outdated, they're actively holding you back. You spend too much time creating these instructions so they are impossible to misinterpret. You labor to ensure everyone has the correct revision and that all the binders aren’t missing any pages. Most of all, you’re spending more time organizing and fetching these documents than actually using them in production.
BuildOS eliminates these limitations with a fully digital approach:
- BuildOS enables dynamic creation and management of digital work and testing instructions
- The platform captures and systematically documents critical tribal knowledge from your team preventing knowledge loss
- With BuildOS, shipyards gain full digital traceability, enabling them to track components, processes, and quality data throughout the production lifecycle
- Digitally enforced compliance to quality acceptance standards
Ancra Aircraft's transformation demonstrates the power of going digital, not just modernizing their documentation but fundamentally changing their manufacturing performance.
Reclaiming America’s Shipbuilding Heritage Through Innovation
The US shipbuilding industry faces significant challenges: dependence on paper, tribal knowledge vulnerabilities, manual processes, testing bottlenecks, and growing workforce skill gaps. These inefficiencies have contributed to a dramatic decline in global market share and threaten both economic interests and national security capabilities.
However, the path forward is clear. Adopting modern digital tools like BuildOS is no longer just an option but a strategic imperative for significantly improving speed, quality, and global competitiveness. Government initiatives and funding programs aimed at modernizing US shipbuilding provide timely support for this transformation.
For shipyard leaders, managers, and engineers, now is the time to address current processes in light of these challenges and opportunities. Digital transformation offers tangible solutions to longstanding problems, with the potential to revitalize American shipbuilding and strengthen national capabilities.
The future of US shipbuilding lies not in the decrepit processes of the past, but in embracing technological innovation. That journey has begun for all other industries, and shipbuilding is up next.
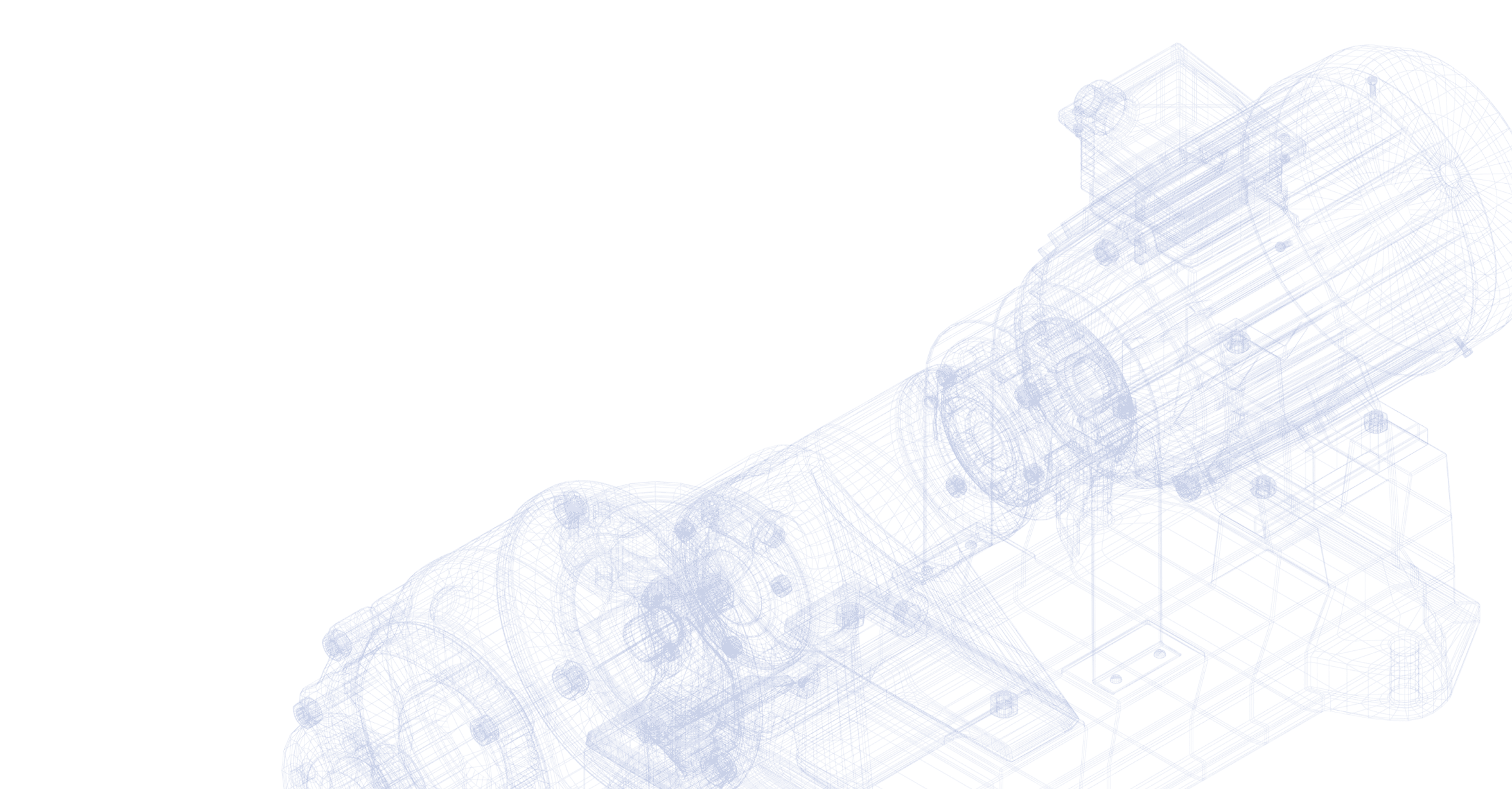
Dirac is the Assembly Company of the future.
350 5th Ave Ste 4720, New York, New York